UNICAN IMMOBILIZER EMULATOR PROGRAM FOR SMART W450 ECUs COMMUNICATING THROUGH CAN BUS AT 500 kbps, REMOTE IMMO SYSTEM.
For proper operation, we need to program the CAN speed at which the ECU operates and the 7-byte synchronization code from the ECU
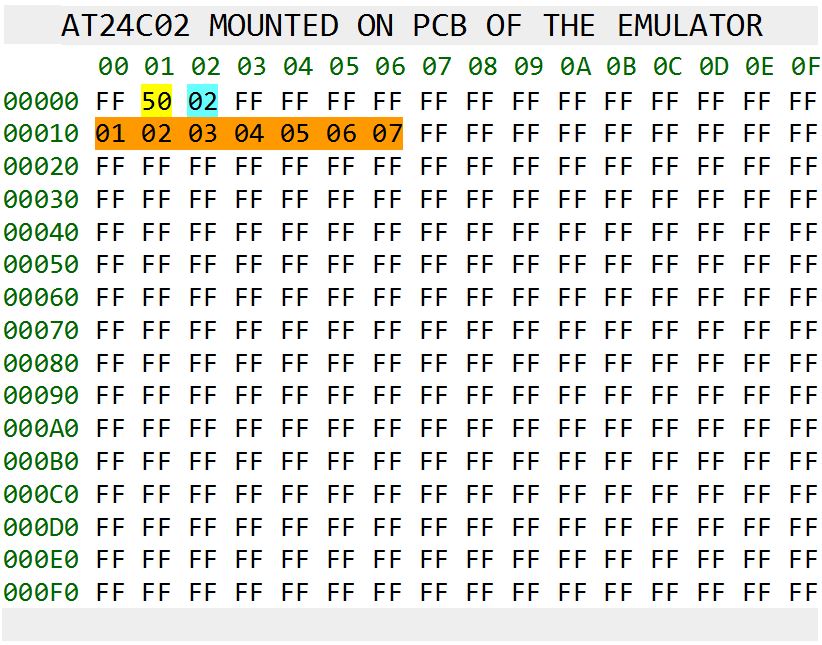
In the cell at address 0x01, we enter CAN bus speed value 50 which gives 500 Kbps.
In the cell at address 0x02, we write the value 0x02, which sets the immobiliser library used in the SMART GEN1 W450.
In cells starting from address 0x10, enter the 7 bytes of synchronization code from the ECU that we intend to unlock.
When providing technical support, we help customers to determine the synchronisation code.
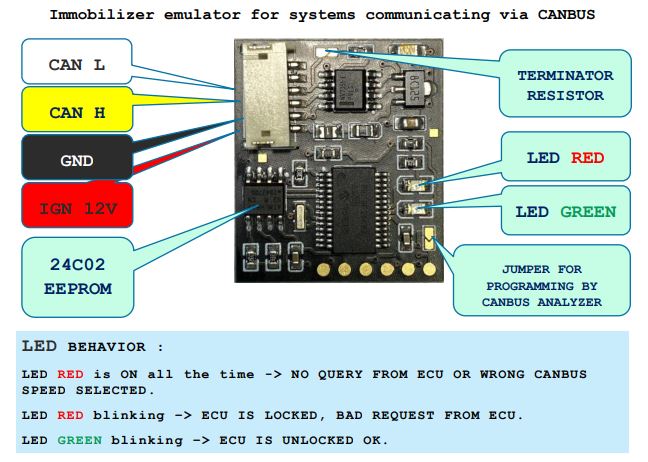
Four wires should be connected: CAN-H, CAN-L, GND (ground) and +12 V IGN ( terminal „15”) or +12 V after the ECU/ECM relay. Ensure the connection adheres to the vehicle’s repair schematics.
The colors of the corresponding wires are specified in the photo.
The location of the eeprom 24C02 memory is also specified in the photo.
Please remember the CAN terminator – terminator resistor, is in many cases indispensable especially when the ECU works standalone.
The description of the green and red LEDs can be found in the photo, thanks to them we can carry out diagnostics of the emulator connection, they clearly indicate the current status of the CAN bus connection and the status of matching to the ECU.
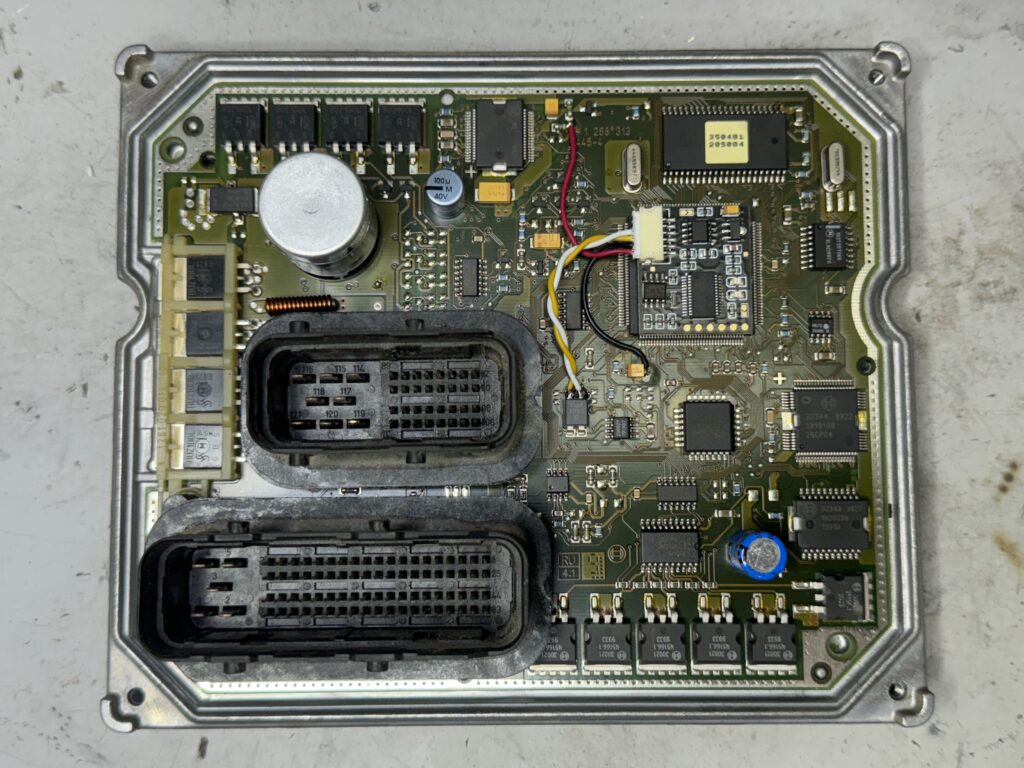
Pictured is the ECU engine controller from a SMART W450, a more frequent visitor to my lab table BOSCH MEG1.X 0261205004, 0261205005, 0261205006.
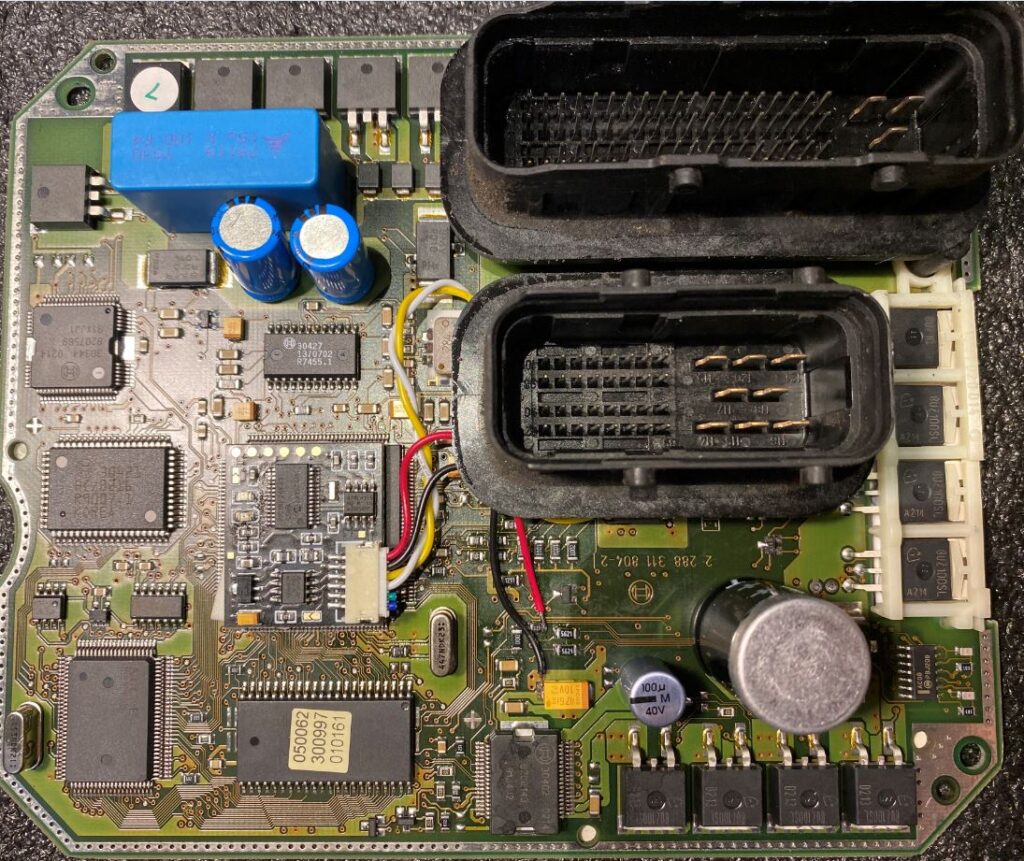
Pictured is the ECU engine controller from a SMART W450, also frequent visitor to my lab table BOSCH EDC15 0281010161.
The emulator works with SMART W450 vehicles with an immobiliser system disarmed by remote control.
EXAMPLE VIDEO USAGE UNICAN EMULATOR ON SMART W450 MEG1.X ECU
In order to use this solution, the customer must be qualified as an automotive electronics technician and have the necessary diagnostic tools and wiring diagrams.
In the event of problems and the need for technical support, a CAN bus analyzer will be required in addition to the ECU files, as well as the ability to operate it.